Plasma Cutting
Plasma cutting can only be used for cutting conductive materials using an accelerated hot plasma jet. Common materials cut with a plasma torch include steel, stainless steel, aluminum, brass and copper, but can also cut other conductive metals. Plasma cutting is widely used in manufacturing, automotive repair and restoration, industrial construction, salvage and scrap work. Plasma cutting is used in a wide variety of applications from large CNC (Computer Numerical Control) applications to small hobby shops due to its combination of high speed, high precision cutting and low cost. The basic process of plasma cutting is to create an electrical channel of superheated and electrically ionized gas. H. Plasma is generated by the plasma cutter itself, forms a closed circuit through the workpiece to be cut, and back to the plasma cutter via a ground clamp. This is achieved by blowing compressed gas (oxygen, air, inert gas, etc. depending on the material to be cut) at high velocity through a concentrated nozzle onto the workpiece. An electric arc is then generated in the gas near the gas nozzle or between an electrode incorporated in the gas nozzle and the workpiece itself, which ionizes a portion of the gas, forming a conductive plasma. To generate enough heat to melt the workpiece , current flows from the mechanized torch to the conductive material At the same time, a high velocity plasma and many compressed gases blow out the hot molten metal and cut the workpiece. H. Cut it apart. Dependding of the power source amperage, Plasma cutting is effective for cutting up to 2-in materials. Hand torches can typically cut steel up to 38 mm (1.5 inches) thick, and more powerful computer-controlled torches can cut steel up to 150 mm (6 inches) thick. [1] Plasma cutters cut by creating a localized “cone” at very high temperatures, making them very useful for cutting sheet metal into curved or angled shapes.
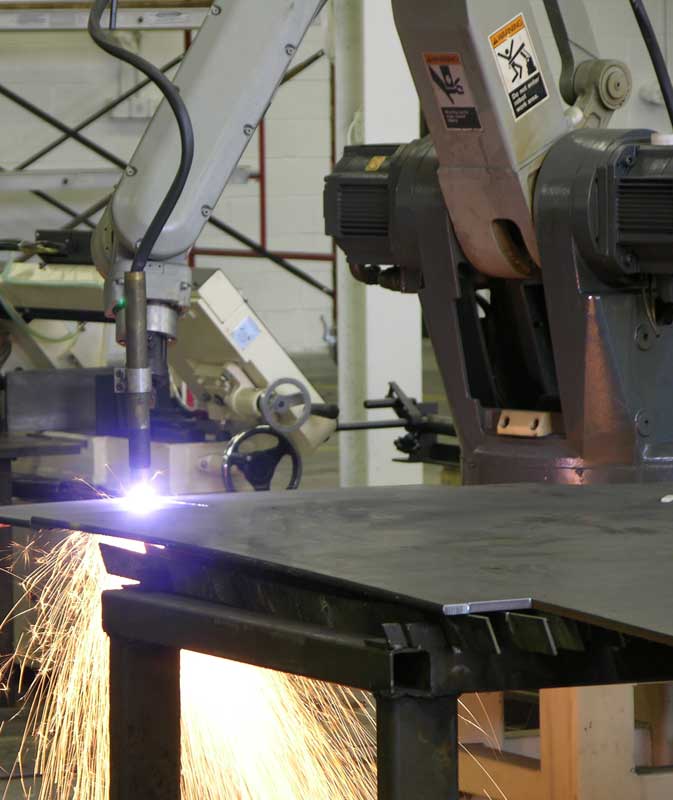
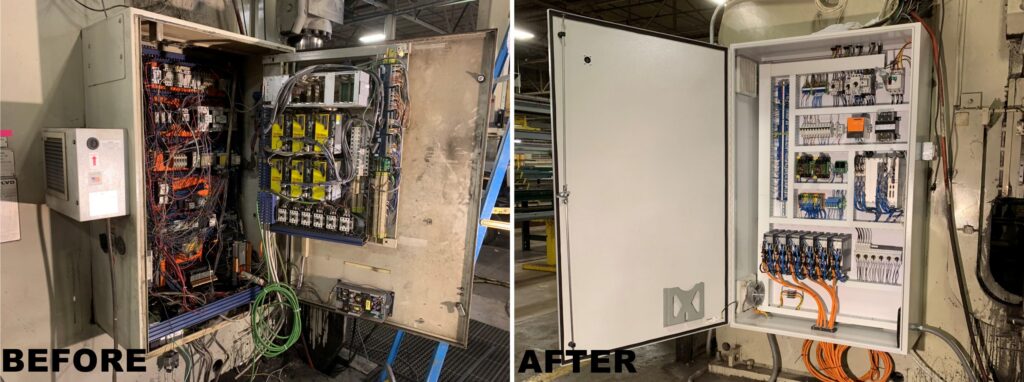
Retrofitting
Retrofitting is the addition of new technology or functionality to an existing vintage machine. Retrofits can happen for a number of reasons, for example with large capital outlays like naval vessels, military equipment or manufacturing plants, companies or governments can retrofit to reduce the need to completely replace a system. Other retrofits may be due to changing codes or requirements, such as seismic retrofit which is designed to strengthen older buildings to make them resistant to earthquakes.