Notre blog
La découpe plasma ne peut être utilisée que pour couper des matériaux conducteurs à l’aide d’un jet de plasma chaud accéléré. Les matériaux courants coupés avec une torche à plasma comprennent l’acier, l’acier inoxydable, l’aluminium, le laiton et le cuivre, mais peuvent également couper d’autres métaux conducteurs. La découpe au plasma est largement utilisée dans la fabrication, la réparation et la restauration automobiles, la construction industrielle, la récupération et la ferraille. La découpe au plasma est utilisée dans une grande variété d’applications, des grandes applications CNC (commande numérique par ordinateur) aux petits ateliers de bricolage en raison de sa combinaison de coupe à haute vitesse et de haute précision et à faible coût. Le processus de base de la découpe au plasma consiste à créer un canal électrique de gaz surchauffé et ionisé électriquement. H. Le plasma est généré par le découpeur plasma lui-même, forme un circuit fermé à travers la pièce à découper et revient au découpeur plasma via une pince de masse. Ceci est réalisé en soufflant du gaz comprimé (oxygène, air, gaz inerte, etc. selon le matériau à couper) à grande vitesse à travers une buse concentrée sur la pièce. Un arc électrique est alors généré dans le gaz à proximité de la buse à gaz ou entre une électrode incorporée dans la buse à gaz et la pièce elle-même, qui ionise une partie du gaz, formant un plasma conducteur. Pour générer suffisamment de chaleur pour faire fondre la pièce, le courant passe de la torche mécanisée au matériau conducteur. En même temps, un plasma à grande vitesse et de nombreux gaz comprimés soufflent le métal fondu chaud et coupent la pièce. H. Coupez-le. Selon l’ampérage de la source d’alimentation, la découpe au plasma est efficace pour couper des matériaux jusqu’à 2 pouces. Les torches manuelles peuvent généralement couper de l’acier jusqu’à 38 mm (1,5 pouces) d’épaisseur, et des torches plus puissantes contrôlées par ordinateur peuvent couper de l’acier jusqu’à 150 mm (6 pouces) d’épaisseur. [1] Les coupeurs au plasma coupent en créant un « cône » localisé à des températures très élevées, ce qui les rend très utiles pour couper la tôle en formes courbes ou angulaires.
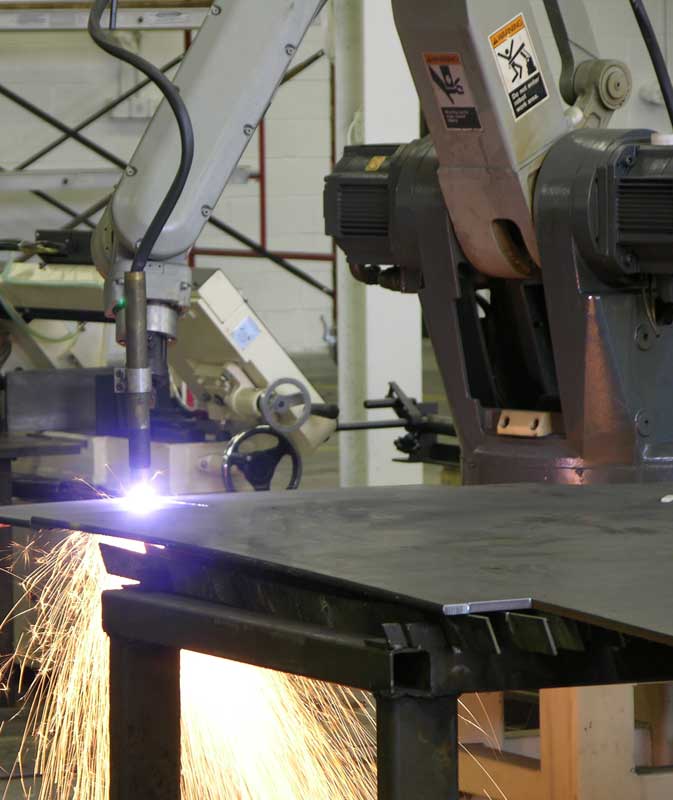
Plasma Cutting
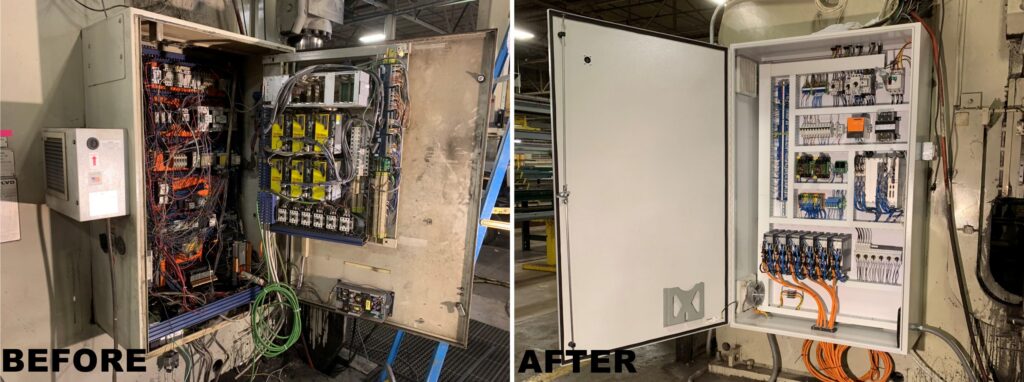
La mise à niveau est l’ajout d’une nouvelle technologie ou fonctionnalité à une machine vintage existante. Les rénovations peuvent se produire pour un certain nombre de raisons, par exemple avec des dépenses en capital importantes comme des navires de guerre, des équipements militaires ou des usines de fabrication, les entreprises ou les gouvernements peuvent moderniser pour réduire la nécessité de remplacer complètement un système. D’autres rénovations peuvent être dues à l’évolution des codes ou des exigences, comme la rénovation sismique qui est conçue pour renforcer les bâtiments plus anciens afin de les rendre résistants aux tremblements de terre.
Fabrication
Le rétrofit est la mesure prise pour adapter de nouvelles fonctionnalités à d’anciennes machines obsolètes
La mise à niveau consiste principalement en des mesures prises pour permettre l’installation de pièces nouvelles ou mises à jour sur des ensembles anciens ou obsolètes.
Les pièces d’adaptation sont nécessaires pour la fabrication lorsque la conception d’un grand assemblage est modifiée ou révisée. Si, après la mise en œuvre des modifications, un client (avec une ancienne version du produit) souhaite acheter une pièce de rechange, des pièces de rechange et des techniques d’assemblage devront être utilisées afin que les pièces révisées s’adaptent correctement à l’ancien assemblage. .
Le rétrofit est un processus important utilisé pour les vannes et les actionneurs afin d’assurer le fonctionnement optimal d’une installation industrielle. Un exemple est l’adaptation d’une vanne 3 voies en vanne 2 voies, qui conduit à fermer l’une des trois ouvertures pour continuer à utiliser la vanne pour certains systèmes industriels.[6]
La modernisation peut améliorer la fonctionnalité globale d’une machine ou d’un système en utilisant un équipement et une technologie avancés et mis à jour, tels que l’intégration d’interfaces homme-machine dans des usines plus anciennes.
Avantage des rétrofits de fabrication :
-Économiser sur les dépenses d’investissement tout en bénéficiant des nouvelles technologies
-Optimisation des composants de l’usine existante
-Adaptation de l’usine pour des produits nouveaux ou modifiés
-Augmentation du nombre de pièces et du temps de cycle
-Disponibilité garantie des pièces de rechange[8]
-Coûts de maintenance réduits et fiabilité accrue
Rétrofit
Démonter les anciens équipements
Définir les E/S (entrée et sortie)
Installer un nouveau moteur, un boîtier électrique et un contrôleur
Passer le câble
Allumer le jet d’eau
Installer le logiciel
Vérifiez la machine pour la dernière fois
Retour à la fabrication
Former les contrôleurs IHM avec votre équipe
Démonter les anciens équipements
Nous sommes arrivés sur le site la semaine de l’installation et nous nous sommes mis au travail ! Nous mettons la machine hors service et retirons l’ancien équipement. Nous retirons l’ancien contrôleur, le moteur, le câblage et le boîtier électrique. Les fils et les câbles sont soigneusement retirés.
Définir les E/S (entrée et sortie)
On passe ensuite à l’étape suivante pour définir toutes les entrées/sorties (entrées et sorties) que l’on va réutiliser. La plupart du temps, nous pouvons tout réutiliser. Installer un nouveau moteur, un boîtier électrique et un contrôleur
Ensuite, nous avons installé de nouveaux moteurs, des boîtiers électriques et un contrôleur CNC ServoTouch. L’équipe a acheminé tout le câblage du moteur de la machine au VFD ou au contacteur approprié. dans le coffret électrique.
Passer le câble
Après avoir installé le nouveau matériel, nous procédons au câblage et à la configuration. Nous acheminons tous les câbles du moteur de la machine vers les VFD appropriés et modernisons toutes les E/S existantes que nous réutilisons. Dans le processus, nous mettons également à jour le schéma de câblage de la machine CNC à partir du manuel d’utilisation. Nous laissons toujours le schéma électrique complet au client lorsque le travail est terminé.
Allumer le jet d'eau
Après avoir terminé la configuration du câblage et du matériel, nous alimentons la machine CNC ! Notre équipe fait une liste de contrôle préliminaire pour s’assurer que les bases sont correctes, telles que les mouvements x, y et z de la machine. Pendant cette période, nous veillons à ce que tout se passe bien.
Installer le logiciel
Une fois que nous aurons confirmé que tout bouge, nous commencerons à configurer le logiciel. Nous configurons la direction axiale, la limite de dépassement de course, le logiciel et la limite IO. Vérifiez la machine pour la dernière fois
Une fois la configuration du logiciel terminée, nous vérifions que tous les boulons sont serrés et que tous les capuchons ont été remplacés. Une fois confirmé, nous serons prêts à réintégrer le système modernisé dans la production.
Intégration en production
Notre équipe d’installation prend les fichiers g-code existants et charge tout dans la machine. Ensuite, nous coupons quelques pièces de test pour nous assurer que tout fonctionne correctement. Une fois que nous avons confirmé que la machine coupe correctement, nous passons à l’étape finale et finale de notre processus de mise à niveau de la machine CNC. Entraînez-vous avec votre équipe
Le dernier jour de l’installation, nous passons du temps à trai